Keeping stock management in the loop
HUS uses consignment stocks in connection to their healthcare facilities to enable easy access to medical goods and supplies, as well as to minimise monetary risks and avoid surplus stock. Before Pagero, however, stock management efficiency was held back by a labor-intensive order-to-delivery process.
“The process was completely manual, thus time consuming,” says Martti Hirvensalo, project manager at HUS. “When a product is taken from the consignment stock, a notification must be sent the supplier so they can invoice us as well as replace the product to keep our inventory at an adequate level at all times. Making a usage notification for medical goods required entry of various data into the ERP system, including lot and serial numbers, along with many other complex steps,” he explains.
Hirvensalo describes even more added work that resulted from a lack of transparency and inventory data: “The first indicator of the goods consumed or used was the supplier invoice. It was only when the invoice arrived that we were able to find out what happened with those goods. Everyone in the industry knows how time consuming it is to manually track purchase order history, no matter how good the routines are. Furthermore, we did not have access to information about the product itself, but rather the purchase transaction.”
“Pagero Mobile has truly been beneficial in improving our requisition and warehouse processes”
Solution found in Pagero Mobile
According to Hirvensalo, HUS found the solution they were looking for in Pagero Mobile, part of Pagero Health Solutions. “It’s a ready-to-use concept,” he says, “which included the very functionalities we needed for removing operational bottlenecks and automating our stock management. Furthermore, it had already been proven effective in its entirety by private and public healthcare providers in Germany. Thus, we introduced the first mobile application to the University Hospital in 2019 and have since gradually implemented the apps into our other units.”
A sharp tool to streamline the order delivery process
Hirvensalo credits Pagero Mobile for a considerable amount of freed resources in HUS accounts payable tasks, including invoice handling and retrospective data imports.
“Using a barcode scanner for sending requisitions means data goes directly into our system and automated internal processes, without manual interference. We can also be sure we have the right product at the right price, and that it is part of the right agreement. And all the data is accessible in our system immediately,” states Hirvensalo.
“Pagero Mobile has truly been beneficial in improving our requisition and warehouse processes. Internally we call the system ‘Sharp’ (Skarppi in Finnish), symbolising a smart and sharp tool. Benchmarked against our manual workflow, we now save several minutes per product, which is a huge improvement,” he adds.
“Working with Pagero has been very smooth and positive, and I look forward to continuing our cooperation”
Transparency and accuracy throughout the process
Hirvensalo points out that automation has brought essential transparency and accuracy into the consignment process. When the data of the product taken from the consignment stock is stored in the system, the identification data of that particular product is simultaneously stored at a specific consumption unit. Consequently, the subsequent traceability of the product becomes easier. In addition, real-time consumption data also improves, keeping hospital stock in balance.
“We also see the benefits of transparency reflected in reduced material error handling. In principle, all the information in the system is correct right from the start. When the barcode is scanned, product information is immediately transmitted to HUS suppliers, assuring immediate replacement of used goods. If the rare error should occur, emending it is a straightforward process thanks to our immediate access to information,” he says.
Get results like HUS
Improved processes for better patient care
Consignment stock goods are mainly used for operations in surgery units. The amount of stock needs to cover every surgery at any given time. When winter arrives, icy sidewalks usually show an immediate consumption peak of certain products. Efficient stock management, however, ensures easy monitoring and that surgeries and operations run smoothly.
“Working with Pagero has been very smooth and positive. With their help, we have been able to take yet another step forward in our endeavor to develop and improve our operations” Hirvensalo concludes.
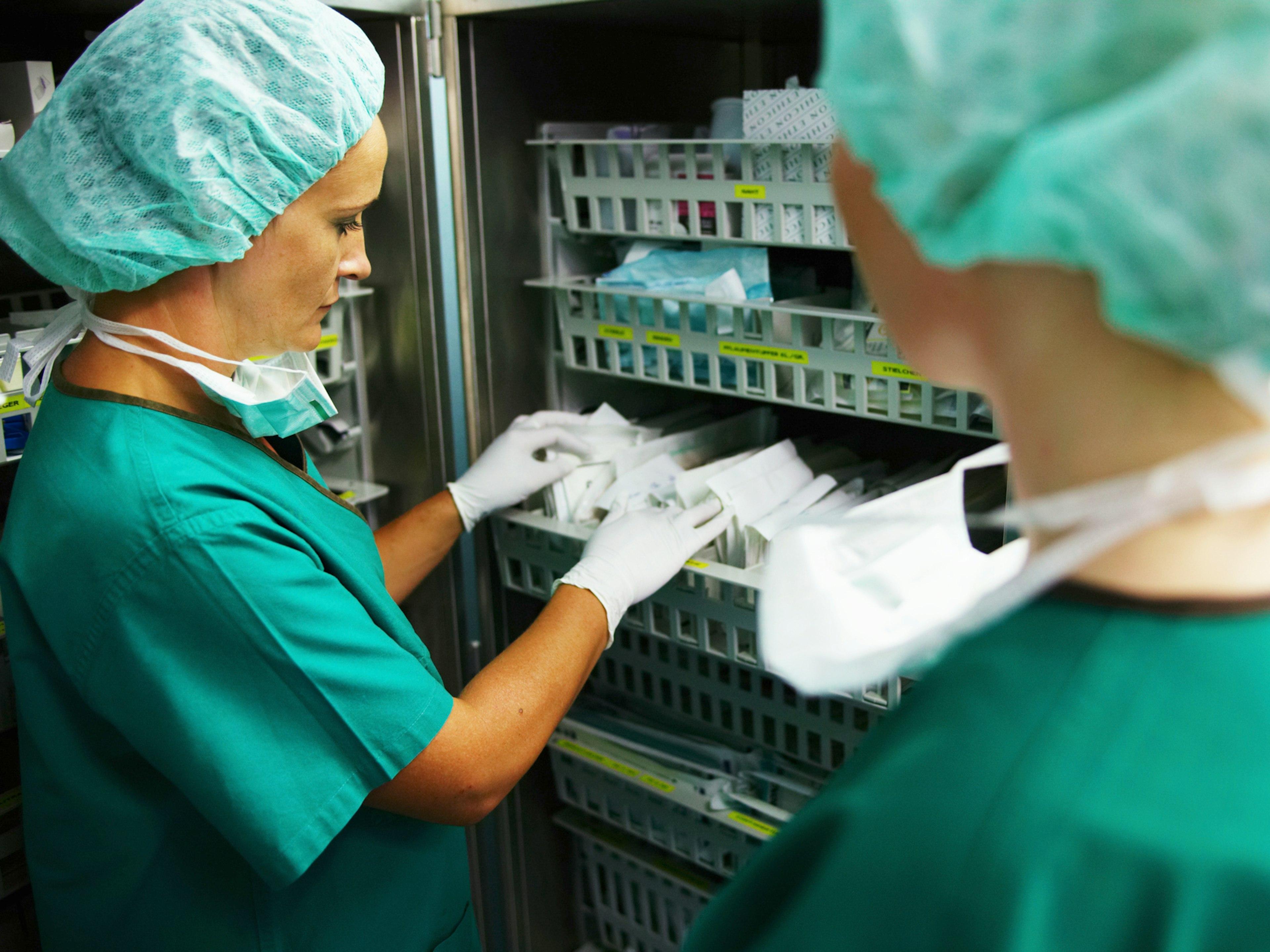
About HUS
HUS, formally the Hospital District of Helsinki and Uusimaa, is made up of five hospital areas: Helsinki University Hospital, Hyvinkää, Lohja, Porvoo, and Västra Nyland. HUS is the largest health care provider and the second-largest employer in Finland. They manage the most demanding specialist medical care in the country and have nationwide responsibility to provide centralised care for many rare and severe diseases.
In cooperation with:
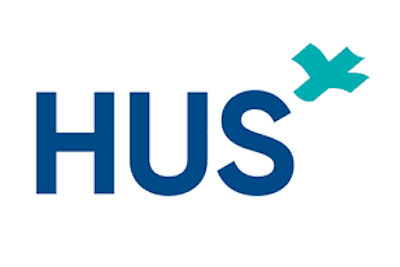
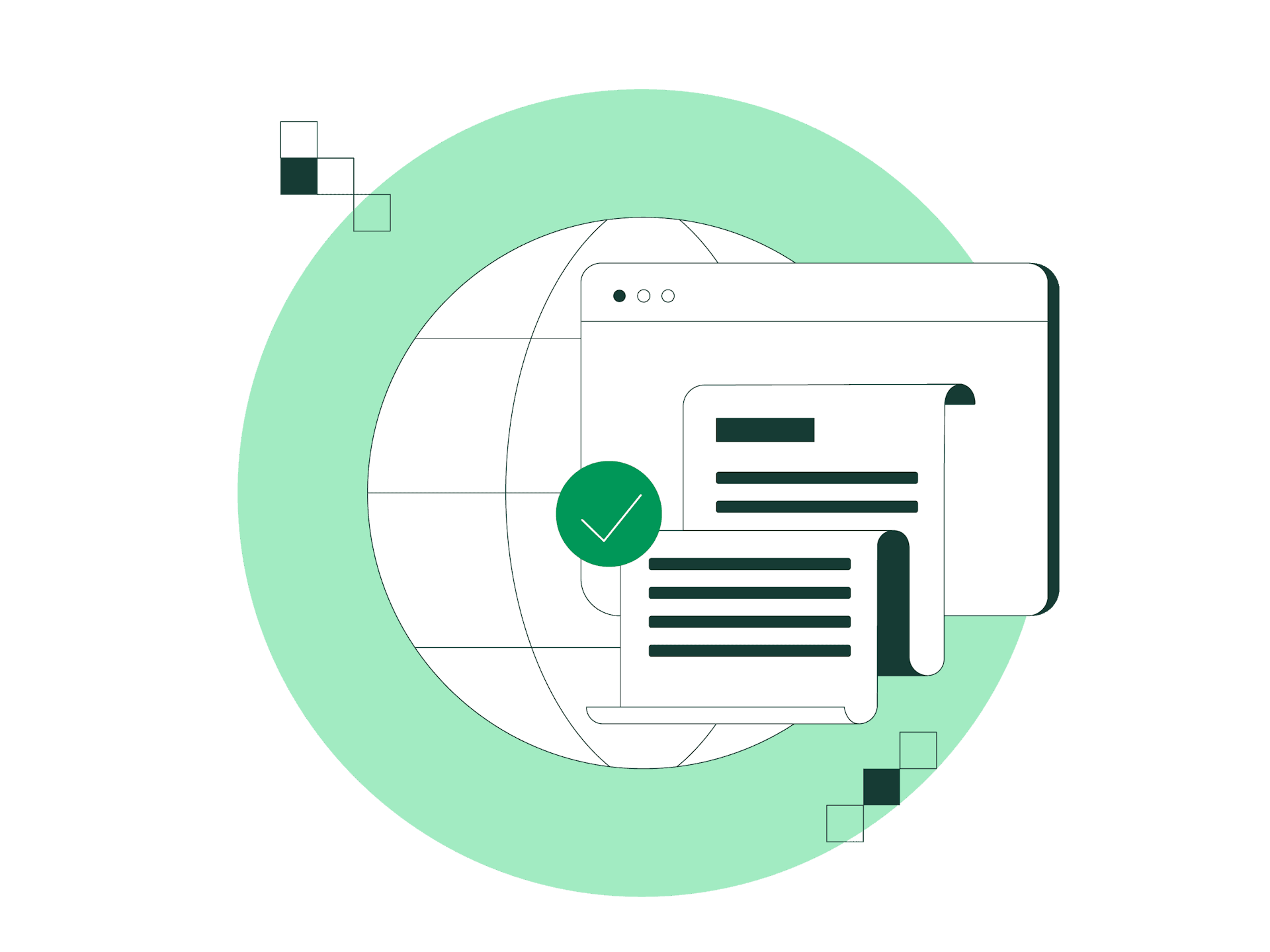
Ready to start digitalizing your business?
Explore more of our resources
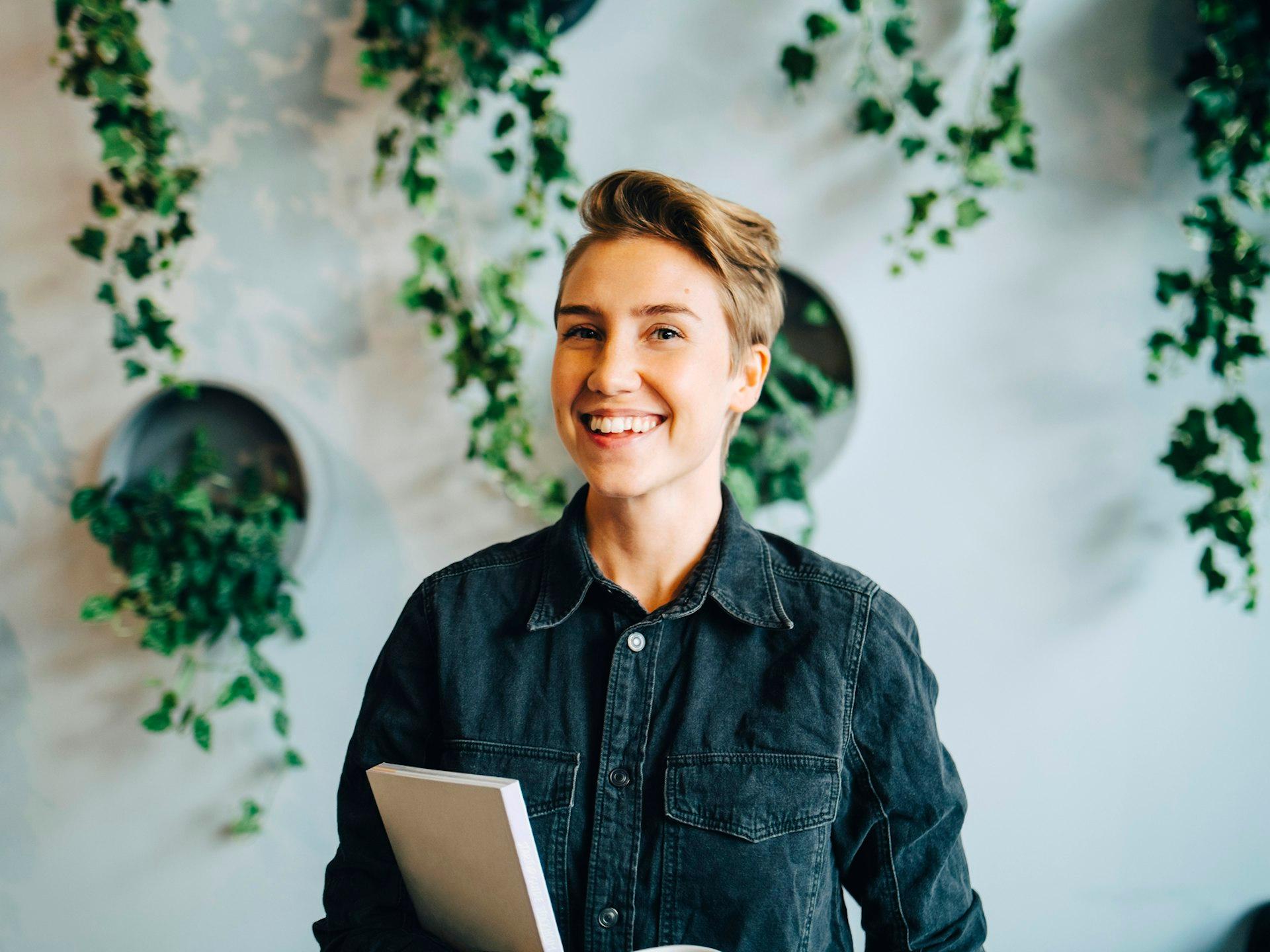